Saturday, December 12, 2015
Friday, December 11, 2015
My friends at Quality Digest were kind enough to publish this great article about the new book, "ISO 9001:2015 in Plain English." A big thanks to Mike Richman (QD Publisher) and Dirk Dusharme (QD Editor in Chief). ISO 9001:2015—An Introduction | Quality Digest
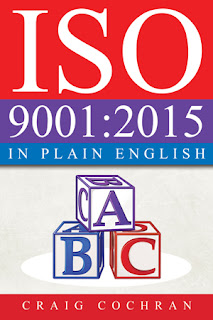
Thursday, October 22, 2015
Records, Retained Documented Information, and ISO 9001:2015
ISO 9001:2015 does a lot of things right, but using clear
language is not one of them. One of the most glaring examples is the
transformation of the word “records” into “retained documented information.”
That’s right, they took one word and turned it into three. And the three words
are not nearly as intuitive as the one word they replaced. Regardless of what
you call them, records are the proof of something happening. They are
historical, referring to past events. As such, they are not revised. Records
might be “corrected” in some cases, but they are never revised. Only documents
are revised. (We’ll address documents and their status in ISO 9001:2015 in a
future article.) The primary control of records is that of housekeeping: knowing
where they are stored, who is responsible, how long they’re kept, etc.
Here is a summary of records requirements in ISO
9001:2015:
·
24 records are required in ISO 9001:2015. This
is compared to 21 records required in ISO 9001:2008. Some of the 24 records
required by ISO 9001:2015 are actually repeat requirements.
·
20% of all the record requirements come from section
8.3, Design and development of products and services. That amounts to 5 records,
which is the same number required by ISO 9001:2008.
·
A completely new record that is required in
9001:2015 is retained information on changes: review of changes, persons
authorizing the change, and necessary actions arising from change (section
8.5.6)
·
ISO 9001 continues its redundant ways. ISO
9001:2015 requires records of evidence of processes being carried out
effectively TWICE, once in section 4.4.2 and again in section 8.1.e.1.
·
More redundancy: ISO 9001:2015 requires records
that demonstrate conformity of products & services processes TWICE, once in
section 8.1.e.2 and again in section 8.6.
·
5 of the records in ISO 9001:2015 have
qualifiers. They are “to the extent necessary” and “as applicable.”
·
One item listed as “retained documented
information” (i.e., record) is actually a document. That is design outputs.
Design outputs are living information such as specifications, engineering
drawings, recipes, formulas, and bills of material. Since they are living, they
are subject to revision, meaning they are documents.
·
A handful of requirements would be virtually
impossible to have evidence of without records, and yet records are not
required by ISO 9001:2015. These include context of the organization (4.1),
interested parties (4.2), planning of changes (6.3), and customer feedback
(9.1.2).
·
One of the strangest record issues of all is the
omission of calibration records in ISO 9001:2015. This has been replaced by the requirement to ‘retain
information on fitness of purpose for measuring instruments,’ which would include calibration. I expect many people implementing ISO 9001:2015 will get a bit confused by this.
Do not let anyone tell you that the “correct” terminology
is retained documented information. If you like that term, then by all means
use it. If you prefer the term ‘records,’ you can use that in its place. Always
remember that documents are records are two different things. That one fact
alone will make any QMS easier to use and understand.
Monday, October 12, 2015
Nobody believes in communication more than Darryl Keeler.
As President of Tech Systems Inc., communication is possibly the single biggest
part of his job. After all, Tech Systems Inc. (www.techsystemsinc.com/) is security
systems integrator with employees in over 32 states, Canada, and Puerto Rico. Being
a medium-sized company with business across such a wide geographic has its
challenges. Darryl Keeler long ago decided that robust and continuous
communication needed to be a guiding principle. “Communication is the key
factor in maintaining a high level of employee satisfaction,” Darryl assured
me. “And satisfied well-informed employees ensure that we have highly satisfied
clients.” Darryl personally writes the Friday Finale, a company newsletter summary
that ends each week and which goes out to every employee. It maintains a warm touch,
covering birthdays, work anniversaries, and anything personal of importance
that is happening with teammates. It also addresses business updates from the
previous week. TSI Family Emails (TSI stands for Tech Systems Inc) is their way
of communicating items that are of high importance to the entire company, sort
of “red alert” emails. These include process changes, policy changes, and major
customer developments. The TSI Family Emails are one step beyond the Friday
Finale’s in terms of business importance. The Tour De Focus is one of the
company’s most impressive communication processes. This is where Darryl Keeler
travels around the country and meets with every company employee. He simply
sits down and asks for comments or opportunities for the company to improve
based on individual opinions. These are
all captured and recorded, and the leadership team works through all of them
and gets back with the folks who suggested the improvements. This entire list is posted on SharePoint for
everyone to review, and the ideas always number in the hundreds. The employee
portal is the live repository of information that team members use for their
jobs. Only the most current versions of documents are available, and it also
includes phone lists, updates, tutorials, and training materials. Finally, the
leadership team of Tech Systems meets every Monday to go over financials, hot
company topics, and opportunities for improvement. The Monday meeting also
serves as the primary feeder of information into their monthly management
review. Communication is clearly the oil that flows through the engine of Tech
Systems Inc. And the president of the company, Darryl Keeler, is head mechanic
and communicator.
Tuesday, October 6, 2015
Control of production at I. Technical Services
Managing operations can be as simple as ringing a bell.
That’s the philosophy that I. Technical Services has taken in Alpharetta,
Georgia. I. Technical Services (www.itechserv.com)
performs electronic manufacturing services, including PCB assembly, system assembly,
test engineering, repair, and logistics. They compete against low-cost
companies in Asia and elsewhere, so they have to be as efficient and lean as
possible. One of their most efficient processes for managing production is
their “bell meeting.” At 9 AM every morning, their production supervisor rings
a ship’s bell mounted on the wall. All the managers and supervisors assemble
under the bell for a stand-up meeting that lasts about 15 minutes. They discuss
what is running that day, what needs to be shipped, and any obstacles or
concerns. Important notes are recorded on a white dry-erase board right below
the bell. “Everybody leaves that meeting knowing exactly what needs to happen,”
Quality Manager, Hector Rivera, stated. “It’s the best investment of 15 minutes
you can imagine.” Throughout the day, employees refer to the production notes
on the white board, keeping themselves focused on what was agreed to. They ring
the bell again at 3 PM every day, and the key players once more gather around
the bell. The focus of this later meeting is to get everybody caught up on the
current status of production. Where are we right now? What is left to be done?
Will we meet all of our commitments today? Resources are re-arranged, as
needed, and last minute roadblocks are removed. The General Manager, Lauren
Thompson, summarized the process by saying, “When we come together under the
bell, we’re not managers of different departments. We’re a single team working
to wow the customer. It reminds us why we’re there in the first place.” I.
Technical Services has conducted their bell meeting twice a day for years. It’s
a very simple, yet powerful process for controlling production.
Monday, September 28, 2015
Goodbye, Quality Manual

- Structure and contents of the management system
- Road map to lower-level documents within the system
- Company history and background
- Overall process flow of the organization
- Company’s products and services described in a clear, practical manner
- Organization’s strength and capabilities
- What to expect during an audit and how to prepare for one
- Responsibilities and authorities of key personnel
- The scope of the QMS
Sunday, September 20, 2015
Ecolink Inc.’s Quality Policy and Cultural Norms
Ecolink Inc. is small company, but you couldn’t find a Fortune 100 company that takes its organizational culture more seriously. Located in Tucker, Georgia, Ecolink (www.ecolink.com) develops and formulates industrial degreasers and solvents. Maybe not a glamorous business, but Ecolink long ago saw an opportunity to leverage its environmental stewardship and help customers make smart choices. “Sustainability is simply the right thing to do,” the company President, John Roudebush, explained. “Secondly, it gives us a huge opportunity to tap into new business. We get a lot of new customers by saying, ‘We’re here to sell you less and safer chemicals.’ It’s a message the really resonates with the environmental, health, and safety community.” The focus on reduction of environmental impacts became one of the driving themes of Ecolink’s business. When the company implemented ISO 9001, they wanted a quality policy that really set the tone for their business practices and strategy. Environmentalism was one of the key principles that was stressed. Never mind that it was a “quality” policy, the point was that this was a major part of their business strategy and it needed to be highlighted in their policy. As John Roudebush led the company through the development of the quality policy, other important themes emerged. These included work-life balance, positive karma, and high integrity and ethics. The final result was a wide-ranging and unique quality policy that truly fit the organization it was written for.
John Roudebush decided that he wanted to go one step further than the quality policy. What sort of employee behaviors would reinforce the principles this company was founded on? This led to the development of the Ecolink Behavioral/Cultural Norms. They represented a natural extension of the quality policy, but defined actions and behaviors that could be put into practice every minute of the day. Over the years the Behavioral/Cultural Norms grew to 25 specific actions that reinforced the organizational culture that John Roudebush was trying to establish. These included such things as “Check your ego at the door,” “Do what’s best for the client,” and “Create a feeling of warmth in every interaction.” In order to make sure every employee understands the Behavioral/Cultural Norms, Ecolink maintains a weekly schedule whereby each employee gets a turn to discuss what a norm means to them. The employees bring the concepts to life through practical examples of how the norms guide their actions. So, when an auditor asks, “How do you communicate and support your quality policy?” John Roudebush tells them to sit back and relax. It might take a while.

Friday, September 11, 2015
Organizational knowledge and ISO 9001:2015

ISO 9001:2015 has been approved
The ISO 9001:2015 ballot has been approved. There were 75 approvals, 0 disapprovals and 5 abstentions (Canada, Honduras, Kazakhstan, Luxembourg, and Qatar). It is planned at this time that the standard will show a September 15, 2015, publication date and it is scheduled for release on September 23, 2015. (On schedule)

Subscribe to:
Posts (Atom)